Precision molding capability
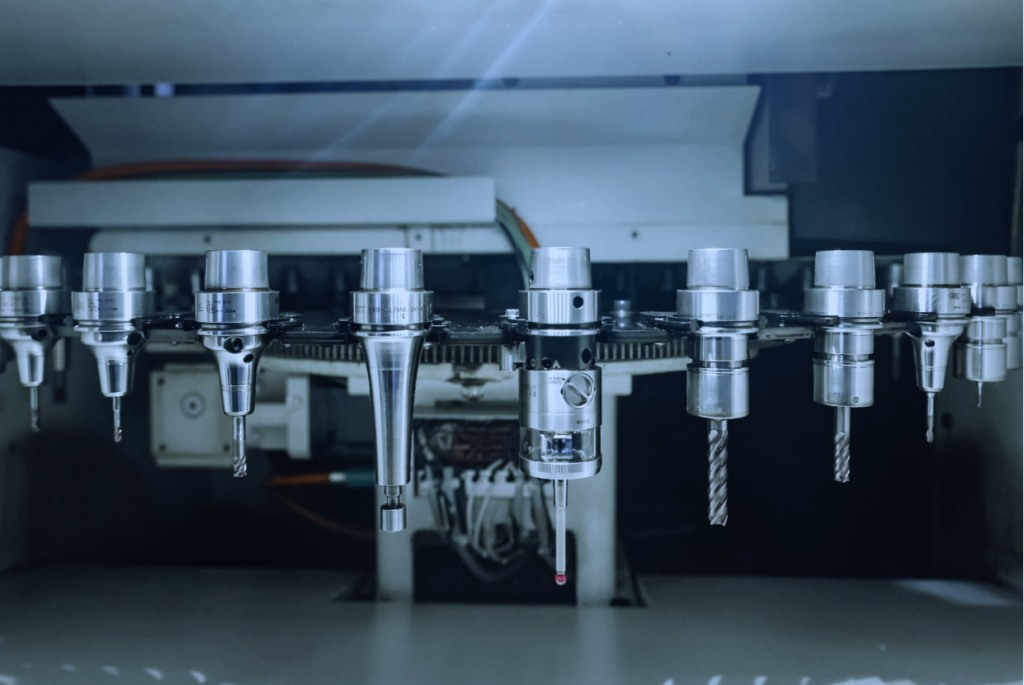
High Precision and Stability
In the manufacturing process of life science consumables, the dimensional and shape accuracy of the product is critical. Our company’s precision mould manufacturing capabilities, relying on advanced CAD/CAM CNC processing technology and top-notch equipment from Switzerland, Germany and Japan, enable us to produce molds with extremely high precision and stability. These molds ensure that every detail of the consumable product meets strict industry standards. Especially in the manufacture of miniaturised and highly complex structural components, our moulds are able to accurately replicate the design requirements and ensure consistent product quality.
Material suitability
Life science consumables often need to be resistant to a variety of chemical reagents and must remain sterile. Our precision moulds are adapted to a wide range of high-performance steels in terms of material selection, and are specially treated to enhance their corrosion and oxidation resistance. These properties ensure a long life of the moulds and do not negatively affect the quality of the consumables during the production process.
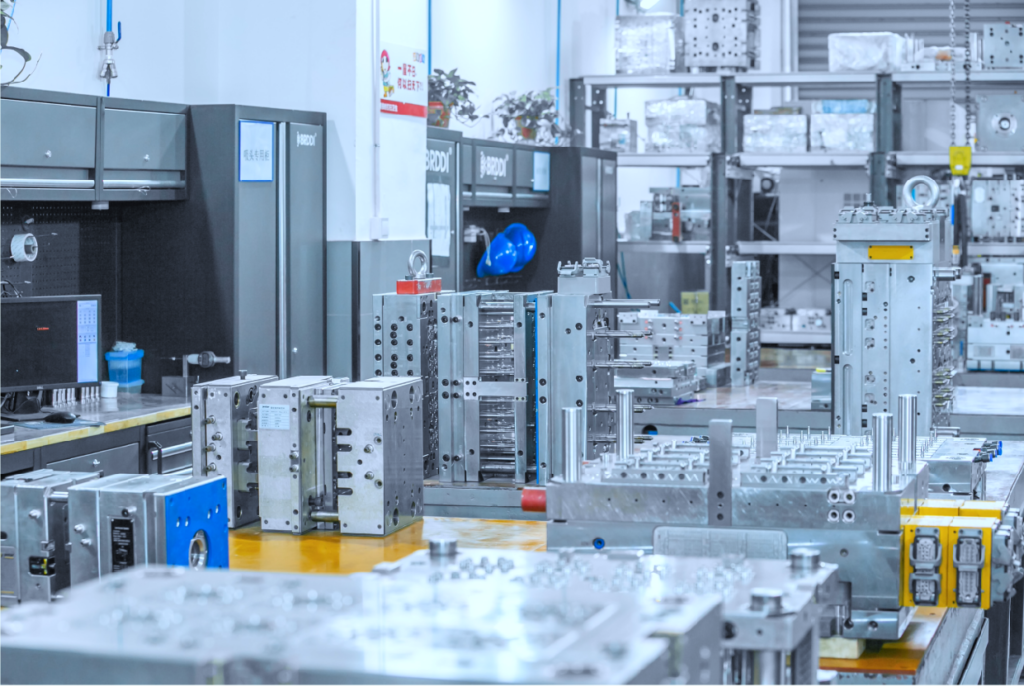
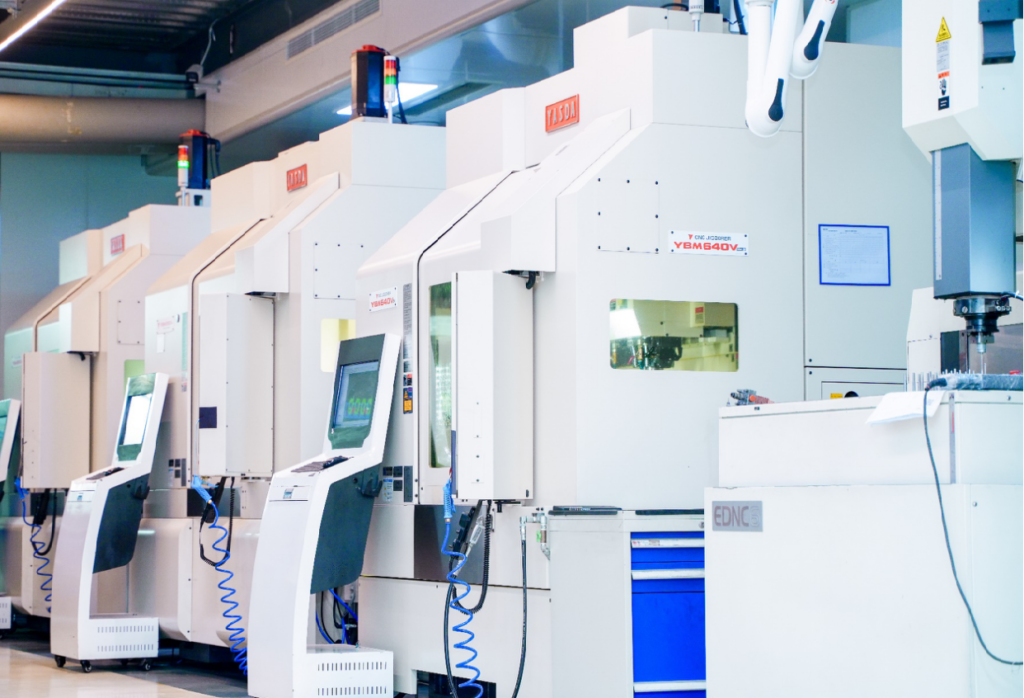
Quick mold change and small batch customisation
We focus on modularity in our mold design, enabling us to carry out quick mold change operations and adapt to diversified, small batch production needs in the life sciences sector. This flexibility enables us to respond quickly to market changes and provide customised production services to our customers.
Precision molding process
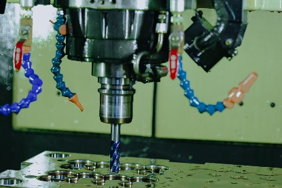
High Cleanliness Production
Life science consumables are usually used in laboratory and medical environments, which require extremely high cleanliness of the production environment. Our company is equipped with a class 100,000 purified injection molding workshop, which avoids any particulate contamination through strict cleanliness control and ensures that the consumables produced meet the sterility standards for medical and laboratory use.
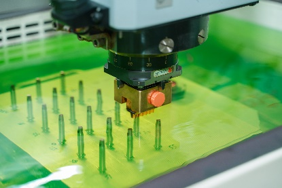
Multi-material Molding Capability
In the production of life science consumables, different application scenarios may require the use of different materials. Our precision moulding process is capable of handling a wide range of high-performance plastics, such as PFA, PP, PEEK, etc., to ensure that the excellent properties of the materials are retained intact during the moulding process. Through precise control of temperature and pressure, we are able to avoid any loss of material properties, resulting in consumables with excellent chemical resistance and biocompatibility.leo.
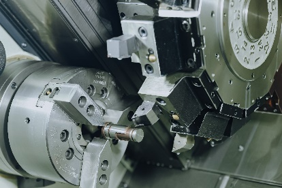
High Consistency with Low Tolerance Control
Products in the life sciences often require extremely high consistency from batch to batch. Our precision moulding process ensures that each batch meets stringent low-tolerance requirements through automated production lines and tight process control, avoiding experimental errors or clinical risks due to batch-to-batch variation.
Coating process
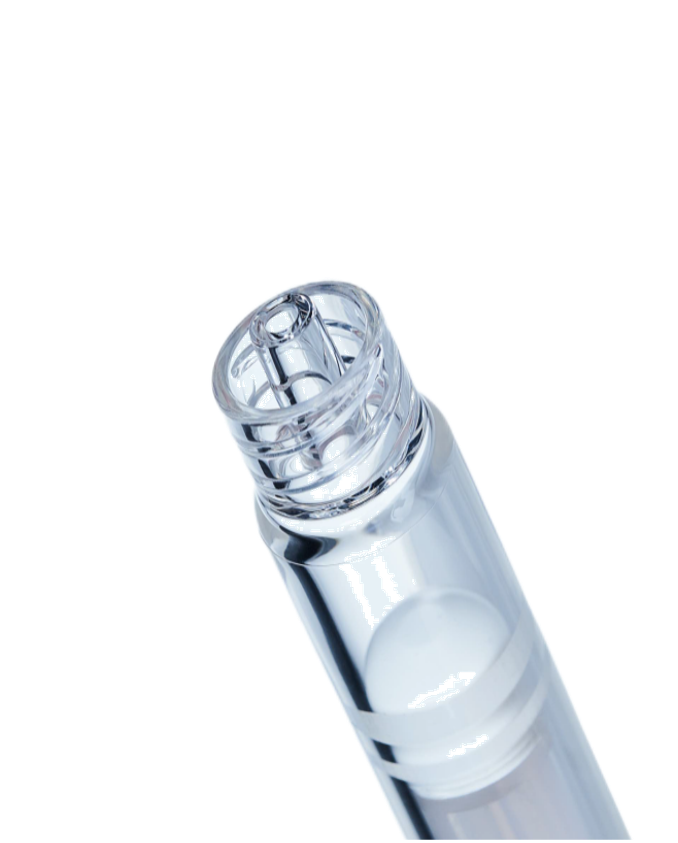
For the specific needs of life science consumables, we offer high-precision surface coating technologies to enhance the functionality of consumables. For example, with specific coating treatments, the hydrophobicity or hydrophilicity of consumables can be improved to optimise their performance in experiments or clinics. These coatings not only enhance product lifetime, but also reduce non-specific adsorption between samples and consumables, improving the accuracy and reproducibility of experiments.
The coating materials we use are carefully screened to ensure that they are non-toxic, sterile and comply with relevant medical and biotechnology industry standards. The coating process is carried out in a clean environment, further ensuring the sterility of the consumables, thus reducing the risk of contamination in life science research and medical applications.
For different experimental needs or medical applications, we can offer customised coating solutions. Whether it’s an anti-static coating, anti-fog coating, or anti-bacterial coating, we can adapt to the specific needs of our customers to meet the requirements of use in specific application scenarios.